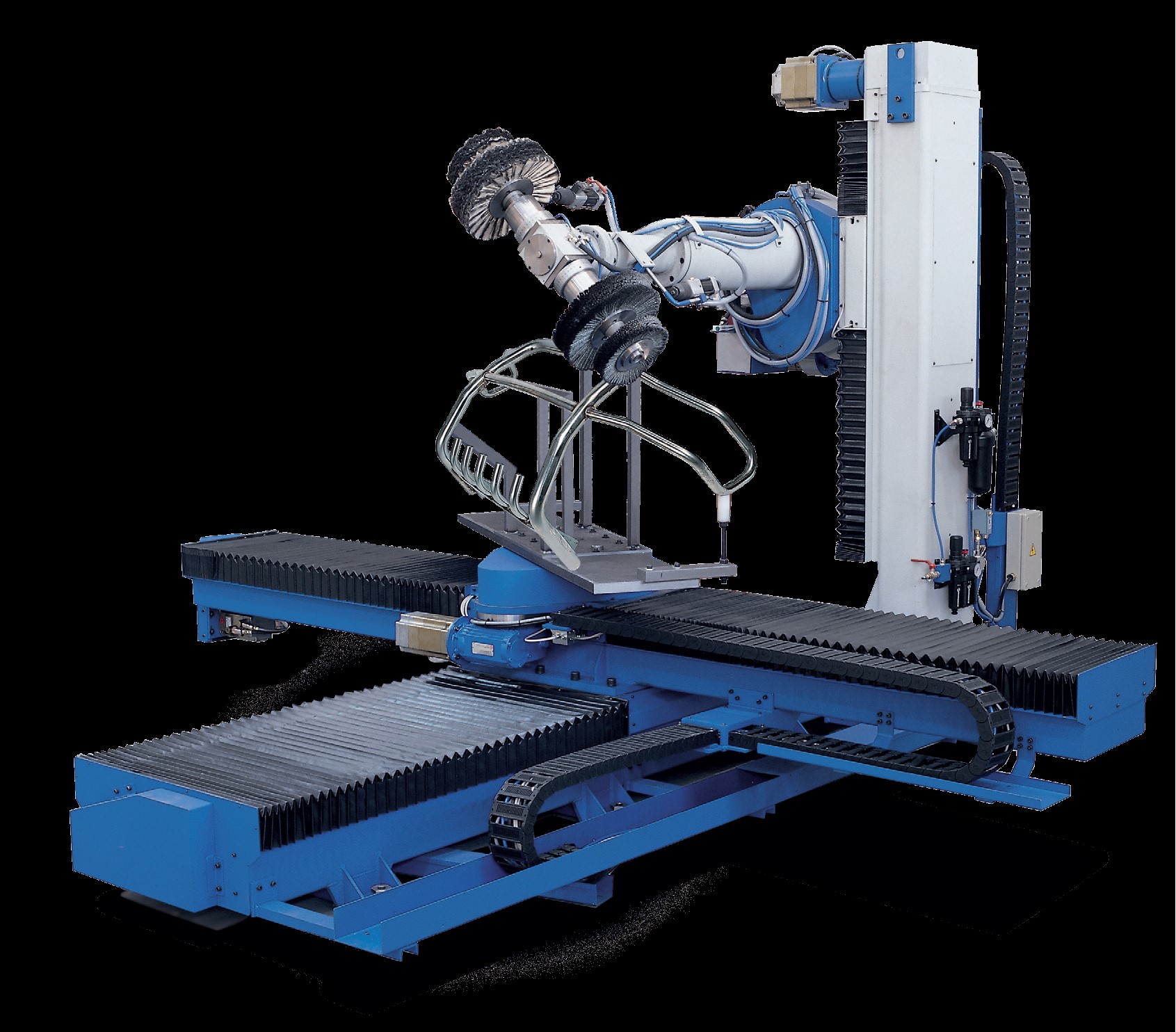
I had a few good questions sent to me on the last entry so I am going to give a bit of detail on one application to better show the process.
The project was for finishing air tanks and gas cylinders. The parts ranged from 14" tall to 49" tall with a diameter range of 10" to 24". There were two operations needed as there were both new and old product that would need processed. The new product was going to be raw aluminum and would need to be mirror polished. The old product would need sanded as a prep for paint. There were cases where new product needed sanded for defect removal but that was simple with the system setup and they would be able to do it on demand.
Reasons for looking at automation, Worker injury was number one. A person holding on to a large tank attempting to polish it on a fixed back stand was causing back injury. Then the tanks that would get away from the workers could end up as smashed feet and hands to much worse. After the worker issues came part consistency. When you have a group of people hand finishing there will be a variance across all of there parts. Then as the day passes and they get tired there will be a variance across each persons parts. That ends up causing a wide swing in the end finishes.
First issue was to come up with a way to hold different length parts. This was not to hard as the very bottom and very top did not need processed. And if it did it would be very few parts so they made the choice to do those few by hand as it was rare. That made it easy to have a base the parts could sit on with a rubber liner and an adjustable arm that would come down from above to clamp the top. This gave all the travel needed for the size range and more so first problem solved.
Second was the decision to mix sanding and polishing or to separate. The final decision was to separate due to the mixture of metals. As doing both steel and aluminum parts would cause cross contamination in a single machine. The last thing you want is random steel dust rusting on the outside of your perfectly polished aluminum tank. The other factor was speed, with two machines they could have one line working old parts while the other worked new parts. This allowed them to get a much higher total part count per hour vs one machine and provided some security with redundancy.
By hand, new parts processed could take 15 to 60 min per part due to the size range. To process old parts was a bit faster at 9 to 45min per part again due to size range. With the final CNC we were processing 2 parts at a time in each machine. The new parts were between 3 and 19 min based on size per cycle with each cycle producing 2 parts. The old parts being sanded were between 2 and 13 min again based on size with 2 parts being done per cycle.
With a little math you can see the volume you can produce with one person. And you get consistent parts with reduced risk to staff. If you look only at the largest old part as an example,you produce two parts every 13 min. Load and unload are quick taking under 60 seconds. So lets say you can produce two parts every 15 min. With an 8 hour shift I will take out 90 min for lunch, breaks, abrasive changes. That would leave you with 6.5 hours of real run time. With 2 parts every 15 min you end up with 8 parts per hour x 6.5 hours = 52 parts per day with one person. When you look at what one person could produce in the same time with the same part working by hand you might get 10 parts on a good day. So you have a situation where each machine did the work of 5 possibly 6 people with just one person. That frees up the others to move to positions or departments where they are needed. You could also add an additional machine later to double the volume if needed. If each person costs $50k with salary and insurances, the 6 hand polishing staff cost $300k a year and that is if you can find them.
In this case it was simple to see that automation was needed. The payback on the equipment was less than a year and they have been in service 7 years so far. That is 6 years of reduced costs and increased profitability and not by a small amount.
I received so many good questions and welcome you to ask yours. just send them to me and I am happy to share what I know. Fell free to send an email to joe at ammachinerysales.com
Topics tube finishingcost of operation comparisonmetal finishingwheelspolishingautomotive