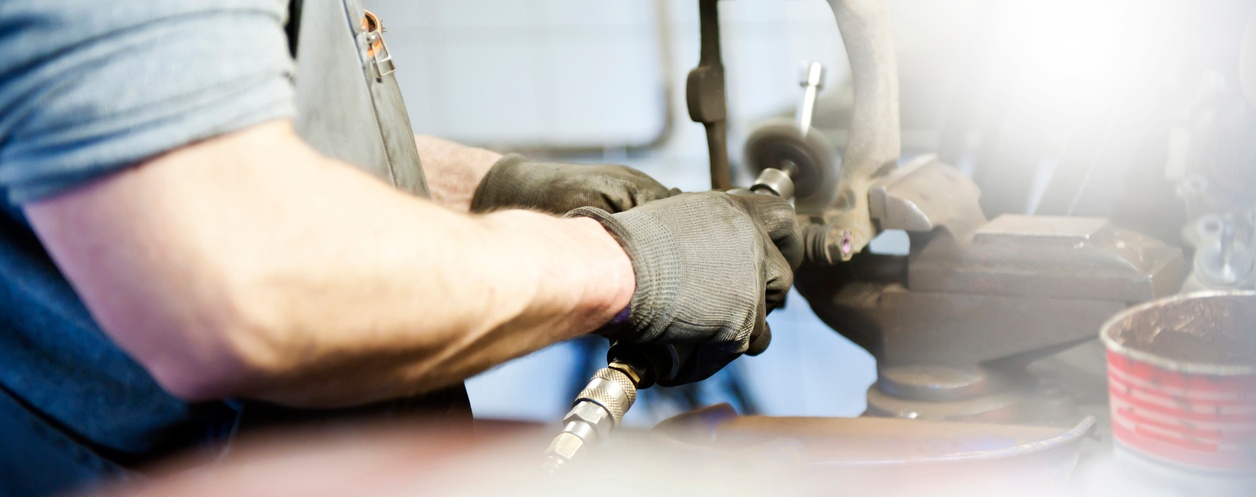
Hello to everyone.
I want to talk a little about an overlooked point but one that I think is very important. Labor is a common topic and one every person who owns or manages a company is aware of. No I am not here to pound on the labor topic in general don't worry.
In every shop there is a person or perhaps you are fortunate and there are several people who have been around some time. It could be a 30 plus year employee that has been working away and knows the job very well. They are the person you lean on when you need something or are in a bind. Well at some point that person will retire and all that experience will be gone.
So what do you do about this? Well you can put an apprentice with them for a year or two just before they leave. There are some issues with that that most will pick up on right away. First is you are now paying two salaries to do one job. That kind of goes against being efficient with your staff. Next is there is no guarantee that apprentice will stay long term so its a bit of a gamble. Then your long term person just may not be a people person and will not take to being assigned an apprentice. Every situation has its details and particulars so the list could get rather long here.
What I would suggest is to store that experience. Rather than have your long term person try and train an apprentice that may walk out at any time train a system. With finishing there is a percentage of it that is an art form. I know that might sound silly but it is true. If you want to see it yourself go find a stroke sander and try and put a perfect finish on a part. It takes practice and learning what the machine can and can not do. There is an art to getting a perfect finish on material be it metal or canvas. You can have all the best tools but if you do not know how or when to apply them you do not benefit fully. Its the old I have an oven in my house but that does not mean I can bake a cake. Knowing how to apply any tool is hugely important.
If you have that experienced person they already know how to get the parts exactly as you need them. They learned all the ins and outs of the tools, materials even what the people in the QC department are looking for. If you can save that experience you have it on tap as long as you need it and it is free from being tied to one person. Letting that experience "teach" a robot for example would be ideal. The robot can mimic the motions of a human arm with no issue. So all the nuance the experienced person learned about holding a tool at just the right angle or moving at a specific speed can be taught to a robot.
You have now stored that 30 years of experience and that employee gets to live on in that company indefinitely. So you store that knowledge and gain all the benefits of automation to boot. You get the parts you want the way you want faster and with more consistency. You are also in a position to avoid the situation where that experienced person leaves and that department suddenly tanks. That is a situation I have seen many times first hand. You know they are leaving but you are not sure what to do. Or you have two other people that work next to them so you think you will be fine. The truth tends to be that the experienced person anchors the process and department. They are the one answering the questions and resolving issues and then when they leave things unravel.
So, Yes you can save experience. It may fall into a less talked about aspect of labor but its real and it should not be over looked. So if you look around the finishing area and you have that person you now have a better idea of what you can do. Just be sure to be proactive and not wait till the problem surfaces to act as it could very well be too late by that point.
As always if you have questions or want to dig further on a topic please feel free to reach out.
Topics tube finishingmetal finishingpolishingautomotive