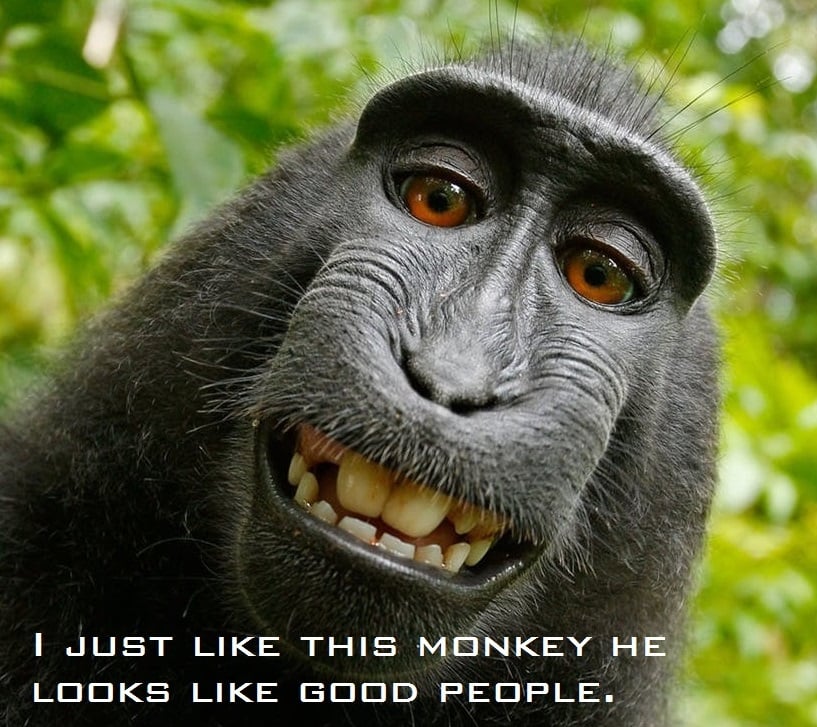
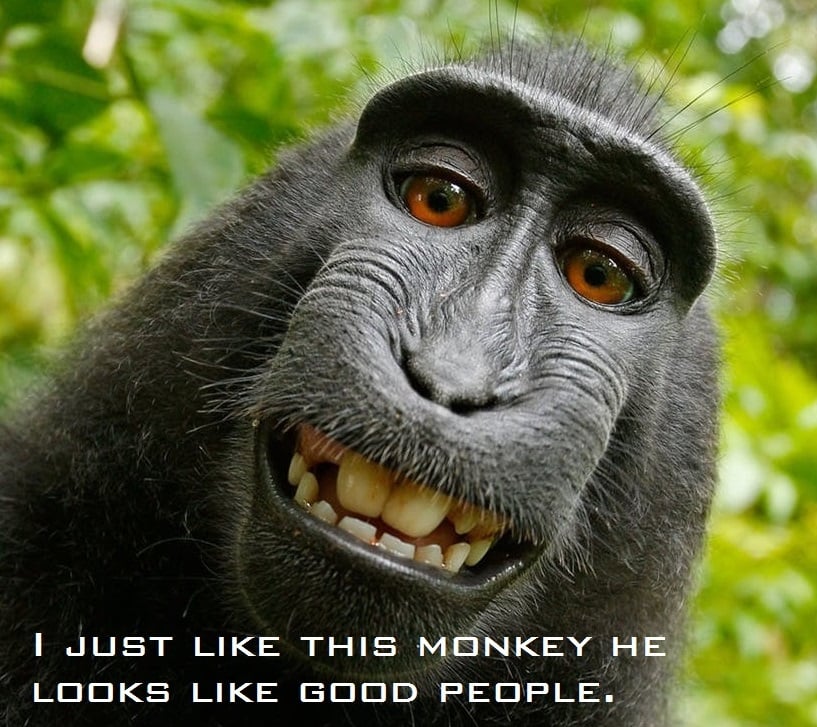
A fab shop can be a crazy place time to time or every day in some cases. You have a shop full of equipment and the staff to match. From your sales staff selling product to the people loading complete product on a truck everyone has a hand in the process. With all the costs involved refining the process and saving where you can simply makes sense.
I talk to a lot of companies and there are a few things I hear often. Some areas have an abundance of labor while others do not and this is compounded by the quality of that labor. Letting a room full of people hand sand parts is not efficient in more ways than one. Getting predictable product while not depending on a large volume of labor is one of every shops goals. Taking the palm sander or DA out of the employee’s hand is a move in the right direction.
The list of reasons could go on for days but I will just touch a few of the issues and concerns that come up most often. Injury be it repetitive motion or the part getting away from them. Accidents happen and no one wants to see someone injured or burned out with a bad back. Consistency is another frequent issue, when an employee starts the day, they will generate one volume and quality, both points tend to fade as the day goes on.
One way to deal with these things is to take advantage of their experience with automation. That person that knows the product so well can be put in charge of a finishing machine to capitalize on their experience. Rather than being leaned over a table with a palm sander all day they can run a machine that finishes the parts. This reduces the injury risk as well as provides a way for them to be vastly more productive. You gain more volume and its more consistent throughout the day. Containing the debris is just an added bonus that everyone can enjoy.
OK, so now comes the question of what machine is best for me. Well, there are ways to finish just about any part from a hand rail that needs sanded to a wheel that needs a mirror polish. The key is to look around and see what all needs a similar process first. One department makes a bunch of brackets or tabs that need a bur taken off. At the other end of the building another department is making trays that need edge rounding for anodizing. These processes could be fed through the same machine rather than getting multiple machines. The key is to identify all of the processes and take a wider look over all to be sure you meet as many of the needs as you can.
There is no one size fits all setup for finishing and it can be complicated sometimes. If you need to process tube that is one machine where sheet metal bur removal is another. Identify your needs first and look to fill as many of them as possible first and foremost. Using every dollar and every employee as wisely as possible go hand in hand. If you have questions or needs feel free to call or send over an email, I am happy to help any way I can.
sales@ammachinerysales.com
Topics metal deburring machinedry deburring machineSmall Part DeburringLoewer Deburring MachinesDiscmastermetal finishing