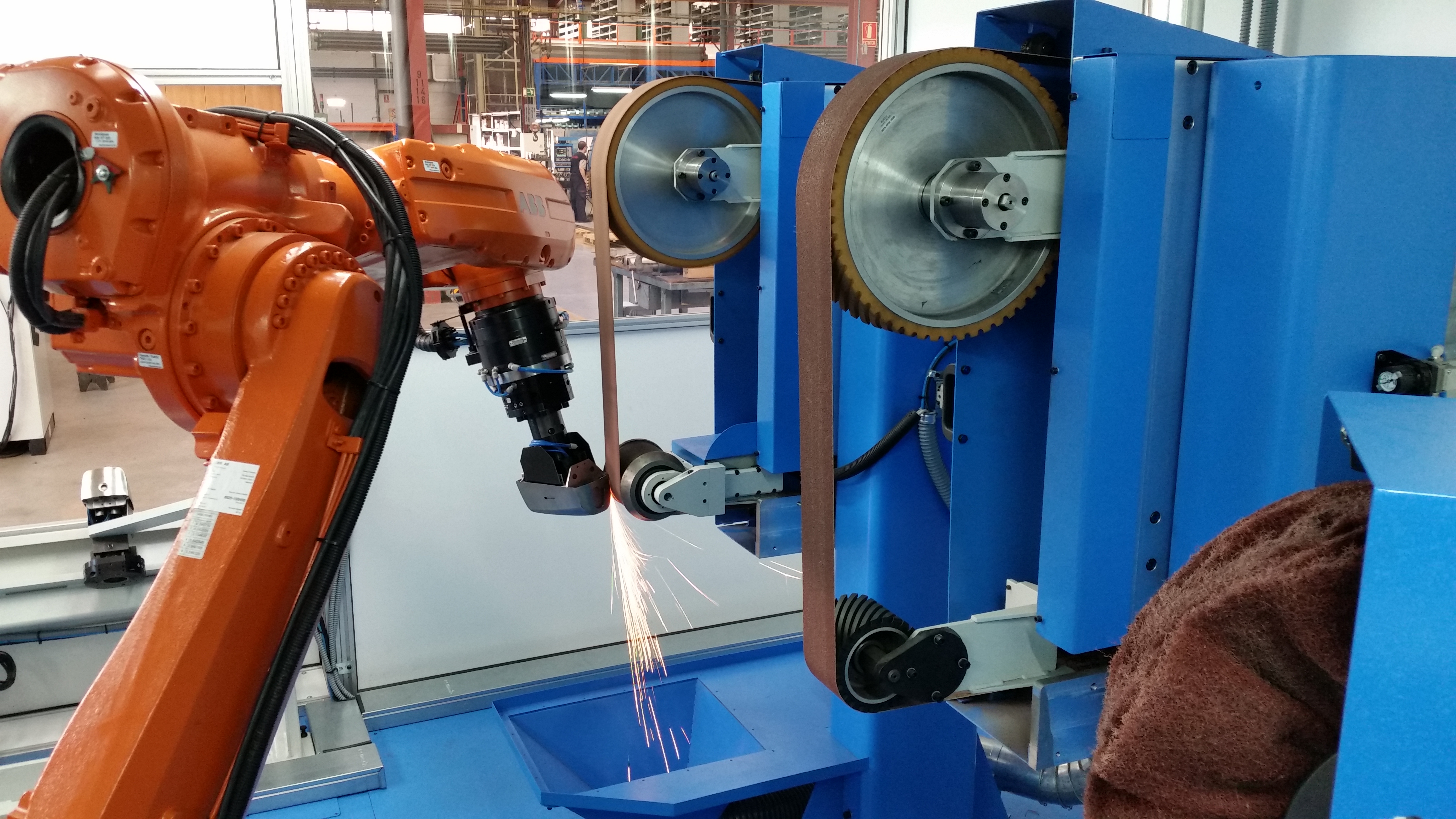
I received so many really good questions I thought it may be helpful to share some with the answer to help others that may be faced with the same questions or problems. I am going to try and not go too deep and keep it easy to understand. Be aware the dynamics of each situation and the parts will be different. Keep sending me those questions as I enjoy good questions.
Question:
How is it you can deal with the variations?
Answer:
Its not a one thing cures it problem. Its much like death from a thousand small cuts. You deal with it by bringing the solution into each facet of the setup. You will make headway in each of the parts to get you the sum total of what is needed. It would start with a good robot. I favor ABB but it is possible with others as well. Things like pressure control in the ABB unit is one of the parts. Building in float to the tools and fixtures is another. It goes on through controlling tool rotation, amperage draw and many others. The key is you have to keep it in mind through the entire process.
Question:
How do you pick the setup? As in do you take the part to the tool or do you take the tool to the part.
Answer:
Its the task that dictates this more than any other point. If you have an electrical box say 24" square and you need to grind outside welds and blend the finish only its simple. Take the part to the tool. The task is straight forward and by doing it this way you can use a full backstand. A full backstand in general produces a better result in these cases and is easier to care for. Even with larger enclosures than the 24" square the answer would hold.
Question:
Why use a large backstand? Save space and use something smaller.
Answer:
You can 100% shrink down the backstands but it will come at a cost. You may gain back space but small backstands have drawbacks. I am not the abrasives expert but I can share what I have seen and experienced myself. Larger backstands offer more flexibility and fewer abrasive changes. When you put together a backstand its not just a sanding belt on some rollers as there is far more thought in it than that. I can use a very soft roller at the top point, a hard roller at the bottom point, a flat platten in the center and areas of free belt in between. I will get 5 or more different tools in one single backstand. A hard roller is good for knocking down a weld quickly. A soft roller will conform more and is better for blending. The flat platten is great for squaring off edges and ends. Free belt is perfect for doing contours and different curves as well as rounding sharp corners. The larger the abrasive belt can be the better. The larger it is the longer it will last between changes and that saves stopping the process. Here is a very good case where experience pays in knowing how to get the most from the tools and how to extend run time.
Question:
I don't have a "programmer" on staff so am I stuck?
Answer:
No your not stuck. In some cases automation is about reducing labor and that is 100% valid. But as a flip side to that it is also about using staff more effectively. You can install 100 new machines and in the end have the same staff count. But rather than 30 people sanding parts you have 2 or 3 running robots and the rest can be moved to welding, assembly, QC, shipping or into the office where they can be more effective. Part of what makes a good system is training. I can train a person to run CNC based systems in a few days with just some basic requirements. With robots it will take a bit longer but in general its getting people past their fear. When people see or hear robot they also think complex and difficult. It takes more time to push that out of peoples heads than teach them to use the robot. Some one who knows the parts and can operate your basic windows computer should be capable of being taught. Practice makes perfect here and it will take some time for them to get fully confident.
Question:
I do more than one part so how many fixtures will I need?
Answer:
Everyone has more than one part so don't sweat this. You will need some form of fixture as that is just the reality. Is there one fixture to handle everything? Well its possible but will depend on what you are working with. If you have enclosures of different sizes its possible to have one adjustable fixture. If you need to do enclosures, counter tops, trim panels and more then there will likely not be one single fixture. Fixtures should always be as flexible as possible to accommodate as many parts as it can but you have limits. The fixture needs to be rigid to get a good finish on the part. If it flexes too much you will get chatter marks or even miss areas all together. There has to be a balance here to keep the fixture strong with a firm grip and flexible to keep fixture counts down.
Those are some of the more common questions and I hope they offer some added insight that might be helpful. As always feel free to ask any questions you have and I am happy to answer them.
joe@ammachinerysales.com
Topics graining sheet metalmetal finishingpolishingautomotiveweld grinding