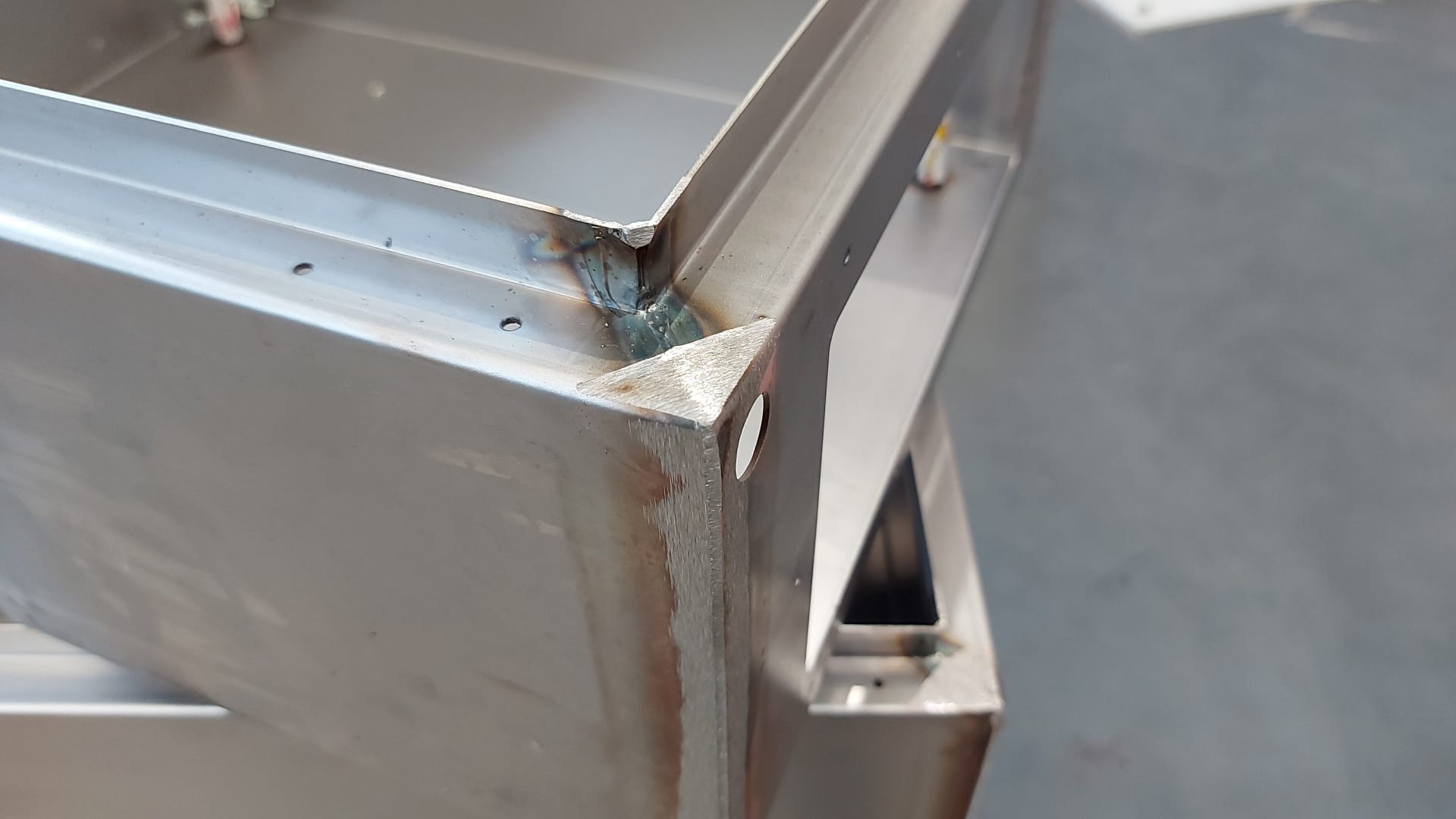
I received many good questions on the robot working with enclosures. To that end I wanted to provide a little more information.
First it was in fact $60,000 a month between scrap and rejected parts. Those are numbers that were given to me by the company themselves. I do not have further data on the exact make up of the amount. While it may sound like a lot I have encountered numbers that were higher.
A mixture of sizes is not a problem. While it can complicate the fixture or table it will not take it to a level that it becomes an issue. The most important thing is to be clear with the sizes you need to process right up front. To go through the process of designing the fixture to only have more sizes thrown in later causes time and money to be lost. Just be clear about the sizes up front and you will be just fine. The odd late part or complete oversight happens so don't worry just be as clear and complete as you can.
The cycle time will depend on what you need. If its a matter of just knocking down the welds with 60 or 80 grit it will be very quick. If you need a fine finish and a radius on the corners that will take longer. But you are talking 30 seconds for the fast process and 60 to 90 seconds on the more detailed. You can take the process as far as you need or want to with the ability to change later.
A mixture of sizes is to be expected and is not an issue. The main thing is that the parts need to require the same process. If you had some that just need a quick pass to knock down welds and others that need mirror polished that would be an issue. As long as the parts all need the same basic process you are fine. You can use bar codes, QR codes and any number of other means to connect a program to a part making it simple for the operators to jump between parts.
With part mixture in mind, The fixtures as well as loading and unloading are taken into account. The goal is to minimize the number of fixtures and make them as flexible as possible. Again this is where being clear on the sizes up front is important.
When you look at enclosures they tend to need the same things. There will be welds that need taken down and a few corners that might need touched to remove sharp points. Having a high paid welder grind the welds after welding is limiting how many parts they can weld. Taking the finishing away from them allows for a higher volume to be fabricated. The speed in finishing keeps that added volume allowing more product to be produced. Increasing volumes and reducing the labor per part tend to be the main starting points. The other things that are farther down the list are things like the mess. Moving the finishing into a robot allows you to contain and collect the debris helping keep the area cleaner. There are many smaller benefits that get overlooked as well as the speed and labor benefits.
Enclosures are a part that is perfect for a robot. You can take the process as far as you want even applying a full brushed finish to the complete part. You can also just quickly knock down the welds just as easy. The volumes that tend to come with enclosures cause labor to swell and limit how many parts can be completed a day. It is an application I work on frequently and tends to be very rewarding.
If you have any questions or need help with a specific issue please feel free to send me your questions or give a call. While robots are not the answer to every question they do have their place and enclosures are one clear place where they shine bright.
Joe Amick
joe@ammachinerysales.com
Topics cost of operation comparisonmetal finishingautomotiveweld grinding