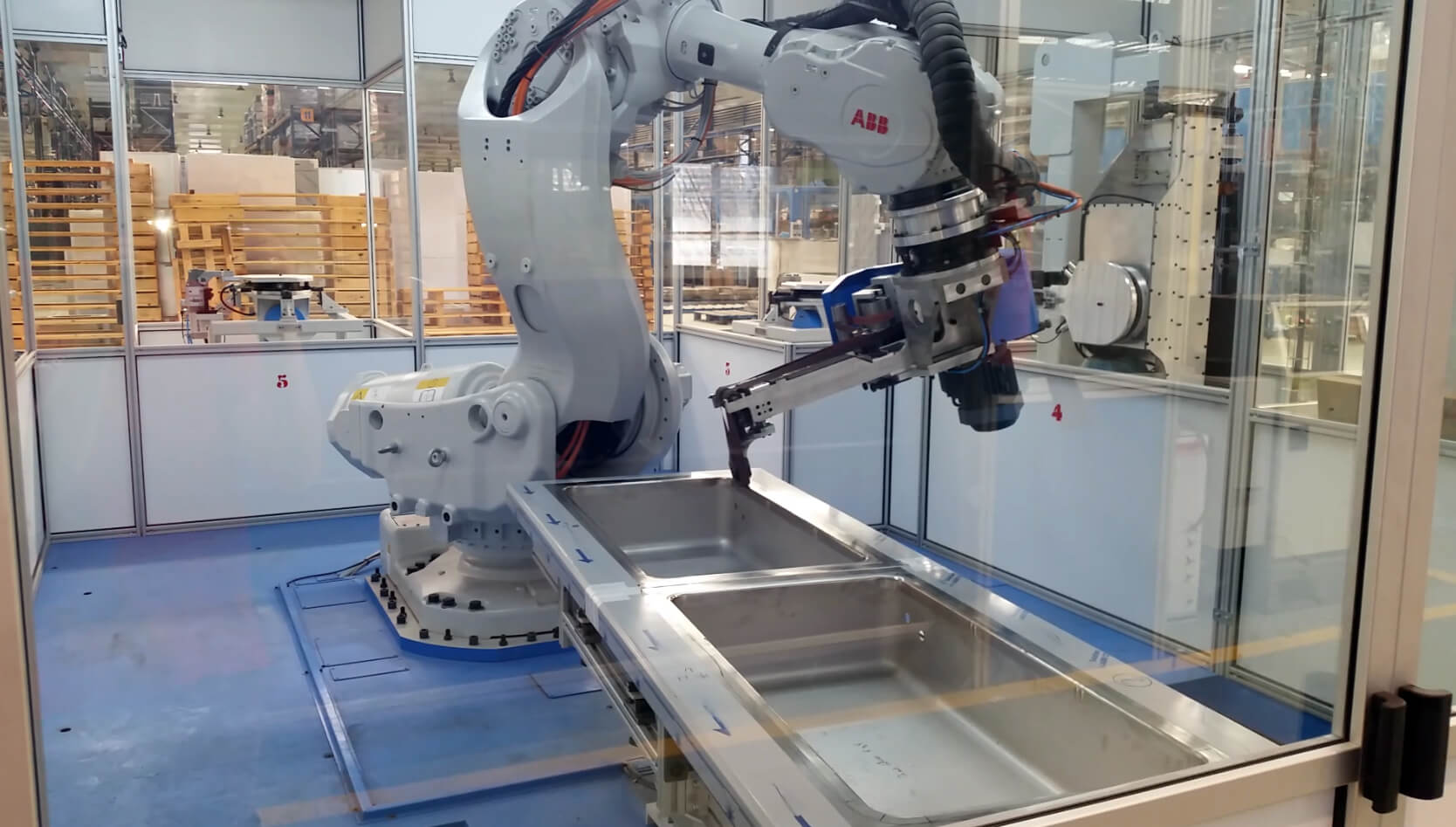
When you start to look into automation be it a finishing application, welding or any number of other processes labor tends to be at the top of the list. There are some things you should keep in mind as you go through the process.
Reducing labor can be a goal but it should be kept in context. It is not about eliminating jobs but affording you the ability to use staff more effectively. Having 10 welders that also need to do the finishing work to what has been welded is not efficient. These people are your skilled welding staff and having them spend half of their day grinding welds is not the best use of their skill or the cost they present the company. To cut the finishing load on the welders you could hire less skilled labor to do the grinding and prep work. Here is where labor savings is cut and dry. You can automate the finishing and avoid hiring on additional labor.
If you currently have a process such as weld finishing that is consuming say 10 total people its not as clear. Labor saving here would be a little different than the example before. Bringing online an automated finishing process would free up 8 or 9 of the people doing the hand finishing. The question then becomes what to do with the people now displaced? Here is where you can use the staff more effectively. The people doing the hand work know the parts very well and what they need to look like. Moving some to quality control positions is one one way to put that experience to use. Using them to supplement raw material handling,shipping, receiving or starting to train them on more advanced tasks like welding. In this situation terminating them would not be the best use of the experience or skill they have acquired.
There will always be situations where termination is the best option. Poor attendance being one of the first issues that will be looked at. If you are working with a temp agency or the like it would be most easy to terminate that contract. But it should be about using the staff more effectively. No one wants to see jobs terminated and that is never my goal with automation projects. Pulling staff from the repetitive tasks that can be automated and moving them to other positions tends to bare the most fruit.
If you need more staff on the bending processes and you cant find more staff then look to free up the staff you have. Allowing people to move positions is a way to get staff where you need with out new hires. Updating a process with new equipment or bringing new processes online are fast ways to free up staff. One welder can manage several welding robots letting one person have the production of many. Same with finishing steps where automating them frees up the welders time to make more product while not needing to hire more staff.
I hear the crowd yelling about the cost of equipment and the headaches of new automation. Yes there is a cost to these things but its a single event. Once you bring that new equipment online and and its paid for itself it starts to add to the bottom line. Bringing on labor on the other hand is an ongoing cost that rarely improves or reduces over time. Making the investment in equipment can carry tax benefits and any number of other benefits as well. Labor savings is about not over inflating your total staff and using what you have in the most efficient ways.
If you have questions always feel free to reach out to me with any questions. I am always happy to look at automation needs and share what I know.
Joe Amick
joe@ammachinerysales.com
Topics Insidermetal deburring machinecost of operation comparisonmetal finishingwheelsweld grinding