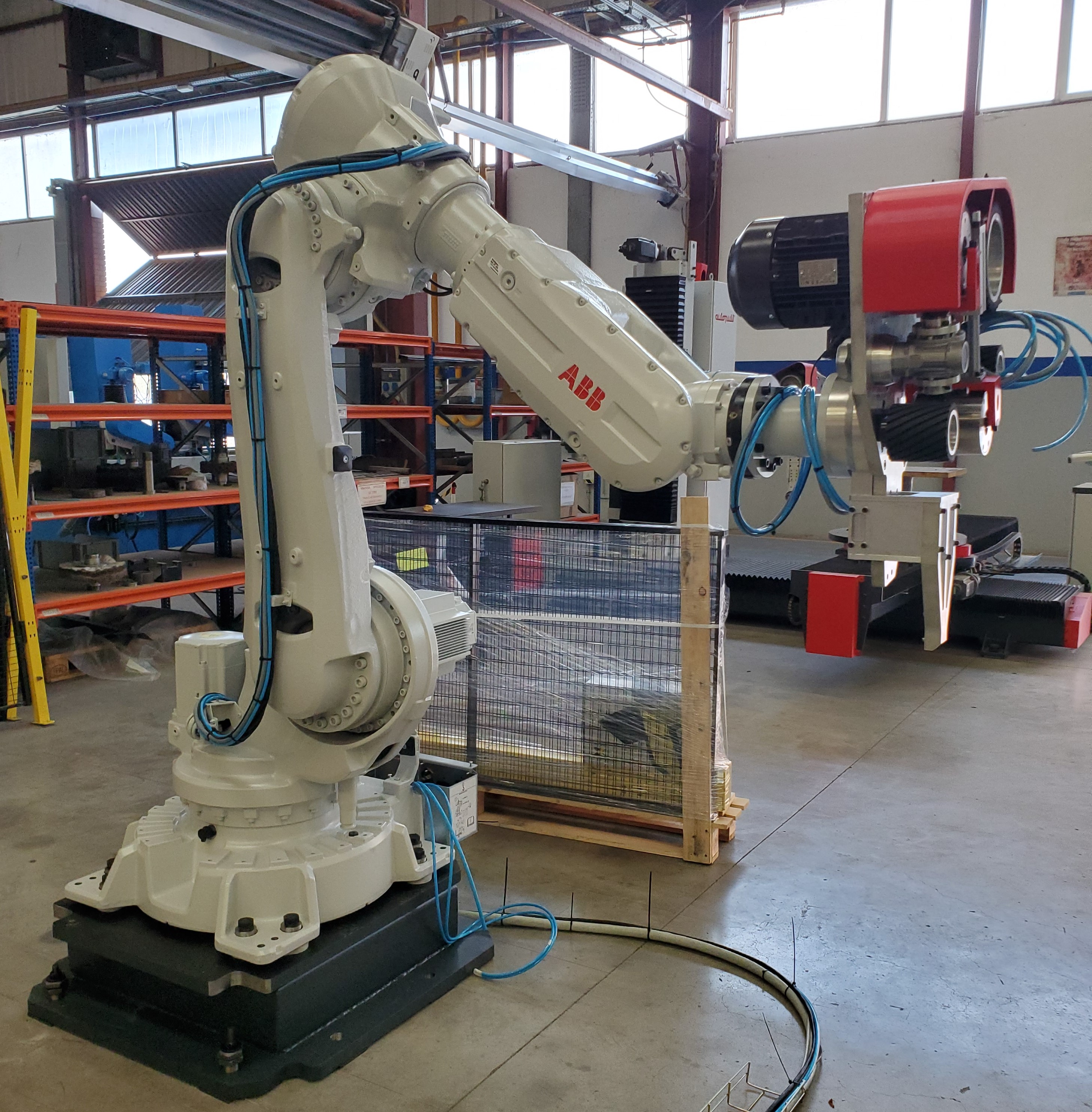
This time I wanted to give a bit of a glimpse into the earlier steps of a new robotic system coming together. If you have never gone through the process it can seem a bit of a challenge. I thought it might be helpful to see some of the earlier steps and I will follow up with it later once it is complete as well.
The application is sanding weld seams on enclosures. There will be standard steel as well as limited stainless steel processed. Some of the main requests were part consistency, reduce hand work and part throughput.
After some testing with the part samples the layout below is what was settled on.
With the part loaded outside the cell it allows the machine to be working while a part is loaded. This keeps the efficiency up and helps keep the operator away from any moving parts. It also allowed us to lower the loading height. Along the same line we are working with a sister company on a system to help lift the larger parts to save any undo stress on the operator. Assisted lifting with an ingenious system that is compact fully customizable requiring no maintenance, I will go into that further another time. The cell then cycles a new part in and a finished part out by rotating the main table. Each part is on a spindle that allows its full rotation so the robot can stay in a fixed position and eliminate the need for an additional axis.
The assembly has just started and it will be around 60 days before it is functional to run tests.
The machine will process a wide range of sizes and is also equipped with a tool changer so the end user can add or change tools later if needed. It is the repetitive day in day out tasks like weld grinding where robots shine. With loading assistance options and a much cleaner workspace its a much better position than hand grinding helping with retention. In this case one operator will produce more parts than 5 people hand grinding and they will all be the same day in and day out.
In this case the company came to me with the parts and a clear description of what the end result needed to be. After running some tests with the parts and putting together a proof of concept for them to see a few revisions were made. This is where it is important to be involved, no one knows your parts better than you. Investing the time into running proof of concept tests will save everyone in the long term. It also allows you the chance to point out any issues or make requests. "Turn key" solutions are not the way to get the very best result. In this case the company was involved and provided solid input all along the way and allowed us to refine the fixture and address the loading before it was even an issue. Be involved is the best advice I can give. Anyone you work with should value your experience with the parts and welcome the input. If that is not the case be sure and ask questions.
I will come back to this once it is up and running to show the final result. In the short term please feel free to ask any questions or send an email if you would like to see larger versions of the drawings or dig further into the topic. I welcome questions and enjoy looking at different applications.
Joe Amick
Topics metal finishingpolishingautomotiveweld grinding