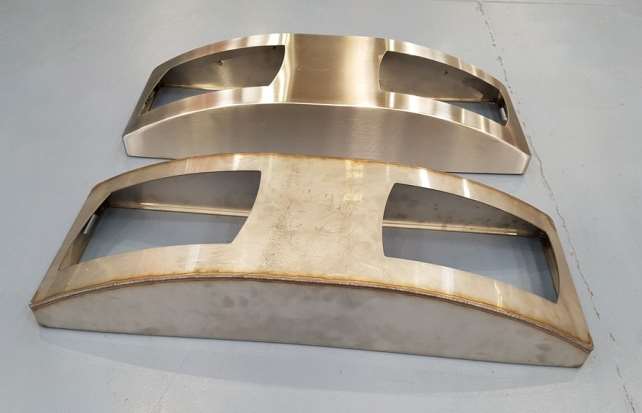
Enclosure and sheet metal finishing has been one of the areas robots make sense. From blending the finish or grinding weld lines they are fast and flexible. One of the first issues you run in to when working with formed or fabricated parts is variation part to part. It can be the heat from welding or the tension in the material or any number of other factors. This has caused many a project to go off the rails. That is not an issue any longer and has been overcome. It was not a one answer solution by any means. It is a combination of fixtures and tools as well as sensors and the feed back loop in a machine. Having a system that can follow the part and deal with the variations is make these systems so efficient. Processing times can be cut to 10% of manual times in some cases with 3 times the speed being the norm. Lights out operation, QC checks, fixture checks, maintenance reminders, automated lubrication the list just goes on and on.
Even with complex curves you can get consistent part quality with out added programming or work on the operators side. The part above is larger than it looks and the manual processing took 40min per part and you did not have the consistency. The same part processed in a machine is well under 10min and you have the part to part consistency. These parts are used in parking terminals.
Range hoods are another very common part I build processes for. The needs and sizes are all over the place but there are a few common points. Weld removal and blending is the most common request. Here again the heat from the weld causes distortion on its own and if it is hand welded there is even more of a variable. These issues have been over come with current systems. Typically these can be processed in a quarter of the time vs the same work by hand.
And yes even the kitchen sink. In some cases its just the top that needs done and in others the complete part needs welds removed and a finish applied. Removing the weld here holds many of the same issues due to heat and distortion. Many parts like this tend to be custom so they are hand welding making it even more inconsistent. Here as well its just not an issue any longer and it is resolved with the same advancements.
Fabricated commercial kitchen equipment? No problem. Counter tops and equipment are both common applications.
Truck bumpers? Again no issue. Here you go from almost 2 hours of manual time down to 18min. The time savings alone are amazing and you get predictable parts. You remove many of the risks to the operators doing the hand work. Back injuries and repetitive motion injures just dissolve.
Do you happen to work with the door that goes with that truck and bumper? Say no more that is no issue as well. You can get the welds done in under one minute.
It comes down to what you need. Automating sheet metal tasks be it formed or fabricated are 100% possible. You can get the speed and part consistency that used to be a myth. As with all things it takes experience and motivation to find solutions to the complex problems. Its a great way to cut labor costs and get higher volumes. So the take away here is don't let the inconsistency in your part or past experiences attempting to automate stop you.
As always I am happy to look at any application and share my experience so ask any questions you have I am happy to help.
Topics cost of operation comparisonmetal finishingpolishingweld grinding