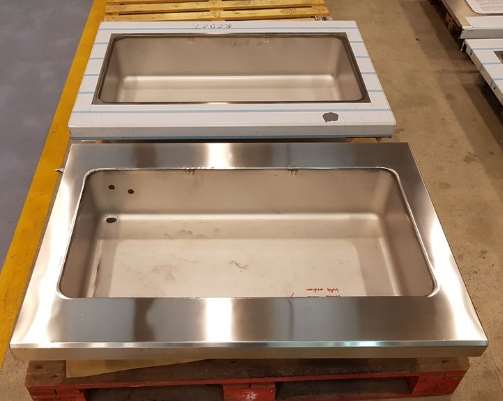
Here we will look at an application where fabricated sinks, counters and other trim parts were finished with a robotic cell. The parts were long term items the company produces where a reduction in labor and an increase in volume were needed. Both were had with a single robot with a tool changer. The ability to grind the weld then shift to blending the finish are one of the reasons robots work so well. It is not a matter of one aspect getting addressed but rather the entire process.
Below is a short video that shows the high points of the process and tools.
The per part cycle times fell by 70% vs the manual process they had in place. It also allowed for more lean manufacturing as they can produce parts on demand quickly. While they do produce stock or standard parts the ability to bring custom parts into the new process allows for quick turn around on orders.
Labor was greatly reduced as was the total time investment per part allowing for greater total volume. The flexibility of the tools allows for several finishes with the ability to change should a new finish be needed. Time was spent making the table as flexible as possible to reduce the fixture numbers down to just a few. QR code scanning from the work orders was used to allow the operator to scan a code and be given the needed detail. It calls the correct program automatically and advises the operator on what fixture is needed. This helps to keep the actual operation very simple and helps to avoid possible issues. There is a second unit being built now for even more volume that will also have laser scanning and camera comparison. This will further simplify the operation as well as allow the system to insure the correct program and fixture are in use. It can also help to further compensate for part inconsistency.
The ability to integrate existing documentation and part tracking are one of the small things that increases efficiency and helps simplify bringing the systems online. The ability to compensate for the variance part to part was a key point here due to the many variables. The heat from welding caused warping and there was some mismatch in material thickness as well. The system has several different ways to deal with these variations and proved to be more than capable in producing even finishes part to part.
In the end the goals were all achieved to a point that an additional system is in production now. The initial leap into these types of automation can be a bit scary and complicated but it can be very much worth the effort. I have covered the things to keep in mind before and they all still hold true. Be clear on what you need and work with some one that has experience.
If you have any questions I am always happy to look at applications even the hard ones.
Joe Amick
joe@ammachinerysales.com
Topics metal deburring machinemetal finishingwheelspolishingweld grinding