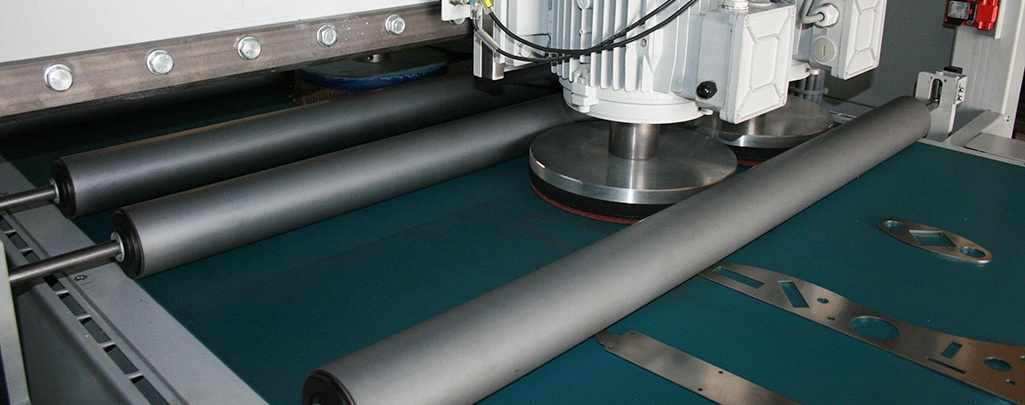
As is always the case looking for ways to save money often leads to looking at many different paths. It can be the time invested in a process to vendor supplies and services. One area to look at that often hides savings is finishing.
If you are sending product out for powder or other coatings what is that vendor having to do to prep the materials? If they are blasting or hand sanding that is costing you per part as nothing is free. Do they guarantee the coating? What is the reject rate? What is turnaround time? If you prep the material beforehand you can more closely control the quality and cost. If the vendor no longer has to do all the prep the cost should go down and the turnaround should improve. Lower costs, faster parts and more consistency can be had by adding or improving the finishing process.
Another aspect is hard savings on the operation itself. As with all things improvements in design and materials take place all the time. There was a time when you would grab a single head "Timesaver" style machine and just throw everything through it. The sharp knife edge often left behind had to be removed in a second step. If the parts were sanded too deeply or with too coarse of abrasive the line or grain finish would show through the coatings when applied. That would be a rejected part or a whole run. Moving to a machine that gives a better key for coatings to bond to without showing through coatings is possible. Avoiding the knife edge made by the abrasive belt means you no longer need an additional step to remove it.
Machines like the DiscMaster from Loewer have a much lower amperage draw so they consume far less power. While savings on the electric bill may not be exciting how about the other costs? If you have a 125 amp load you can't power the machine with lamp cord. To support the 125 amp load you would need at least 4/4 copper cable and even non-UL listed cable starts around $5 per foot. Because it is tied to the cost of copper it varies and in some areas, it can be much more. If you have to run a couple hundred feet you need larger gauge and the cost just keeps climbing. Spending $2,000 or more in just the cable to connect the machine to power is some thing to look at. And if you need a transformer to run that 125 amp load you had better brace yourself.
So, you have a machine bought and paid for, you have an electrician lined up to get it connected and now you need consumables. Well here again is another place to look for savings. Wide belts from 3M can get up near $300 a belt where you can change out the front pads on the Discmaster for well under $50. You can buy super cheap belts made in Asia but you will run through them very quickly. What you save per belt will be lost in the volume it takes to match the good belt. So, saving 50% or more on abrasives is a reasonable thing we see all the time with a DiscMaster.
The take away is to look at the whole picture. Where a machine may seem cheaper on paper in reality could cost far more in the end. Spending smarter to maximize every dollar is everyone's goal. Keeping all the costs both short and long term in mind will help in your choices. Flexibility and utility in any machine are worth far more than a one trick pony.
Topics cost of operation comparisonSmall Part Deburringwide-belt grinding machineDisc MasterDiscmastermetal finishing