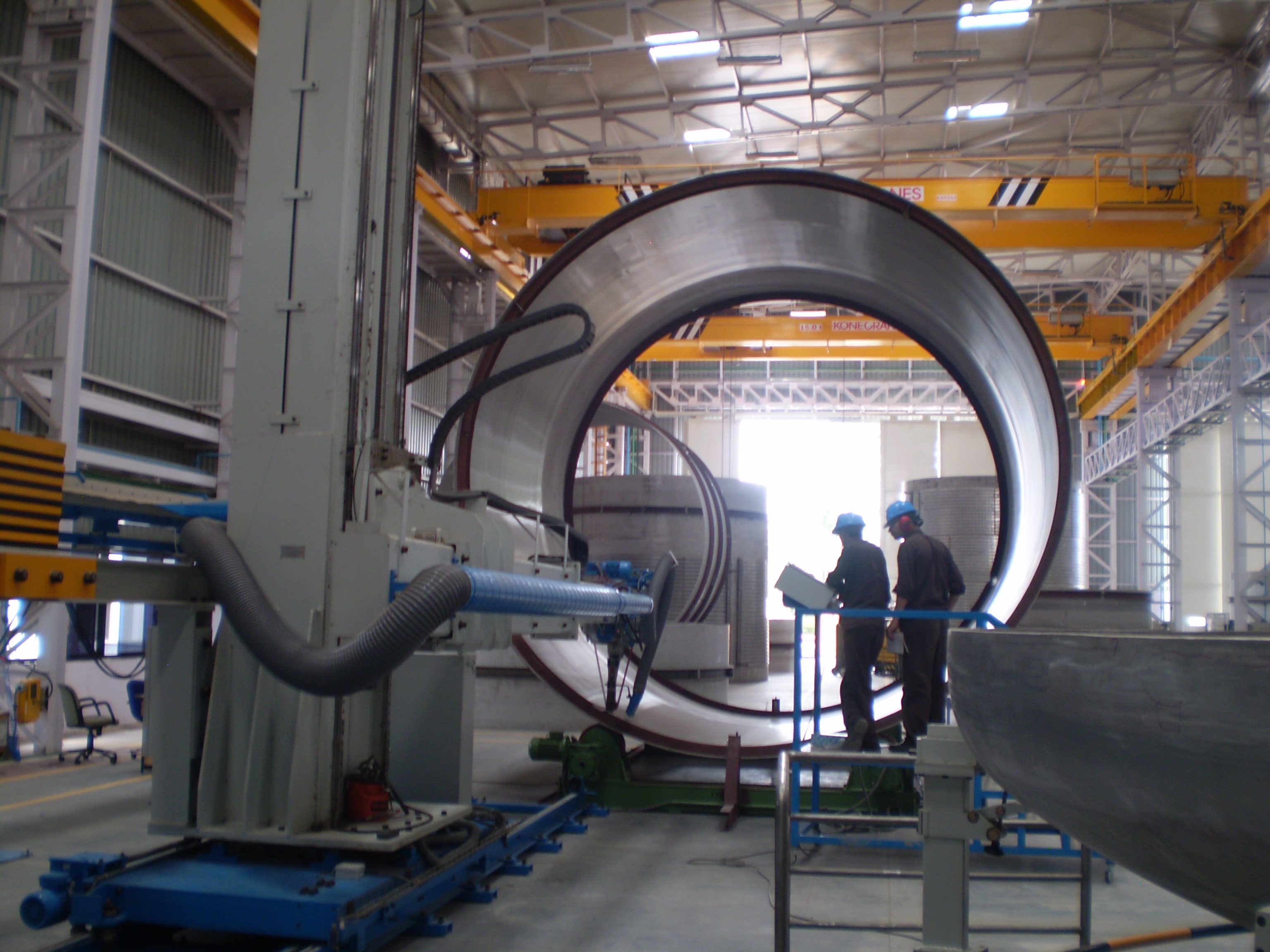
Some of the things to keep in mind.
When setting up a weld removal cell there are some factors you need to keep in mind to have the greatest amount of success. This will just be a brief overview of some of the largest ones to watch out for and pay attention to.
Weld consistency would be the first. When automating weld removal consistency makes things easier.
If the weld is a variable part to part it means you have to plan for the worst case. You need to know you will remove the weld every time and if the weld can be different it makes that harder. It may mean adding an extra pass or slowing the last pass to be sure its gone. This means there are some parts that will be sanded more than they need in order to not have any that are under sanded. Having a constant weld will be a plus.
Working the weld only VS working the whole part.
As is common with range hoods, you peel back some film to do your welds and only sand that area. When you have pre-finished material in these cases you need to match that finish. That can be tough to do as you have such a limited area to do the blend. In some cases its faster and cheaper over all to finish the whole part. If you knock down the weld and apply a finish to the whole thing there is no variance at all. You have a very uniform part over all and some times its faster. When you are not limited to a small area you can make faster movements and be more aggressive as needed to gain speed. You would also save the cost of pre-finished material. It is another decision that needs to be made.
Do not under estimate loading and unloading.
Like the image shows, if you have a large sink to load and unload you need to keep that in mind. How do you move the parts around the building in general? Do you have fixtures that you use while welding? Being consistent and using the same fixtures can make your life easy. You have a fixture and you know it works so why not use it? Rather than design a whole new way to hold the parts look at bringing existing fixtures to the cell. You put the material in the fixture and do your welding, when done leave it in that fixture and send it to be sanded. This is the way some will handle this while others will just make a matching fixture for the cell.
The one thing I often get as a point of worry is the length or general size of the weld.
Size is an issue but not a problem. You can work the weld on truck bumpers or huge cylinders with the same results. Size should not be a roadblock to automation, it only requires the same thought and planning as the weld on a range hood. This is a very good example of the right tool for the right job. Having good guidance and picking the correct system will get you where you need to be.
These are just a few of the most basic points to watch out for and keep in mind. Every cell and every part is unique and there is no one size fits all solution. Ask questions and be involved is the best way to keep things on the right track. With so many years working with finishing and with such a very wide variety of parts I have seen a lot. But I learn new things all the time and that is why experience is such a great teacher. If you have questions I am always happy to talk so please feel free to contact us with any questions you come to.
AM Machinery Sales
Topics graining sheet metalmetal finishingpolishingautomotiveweld grinding