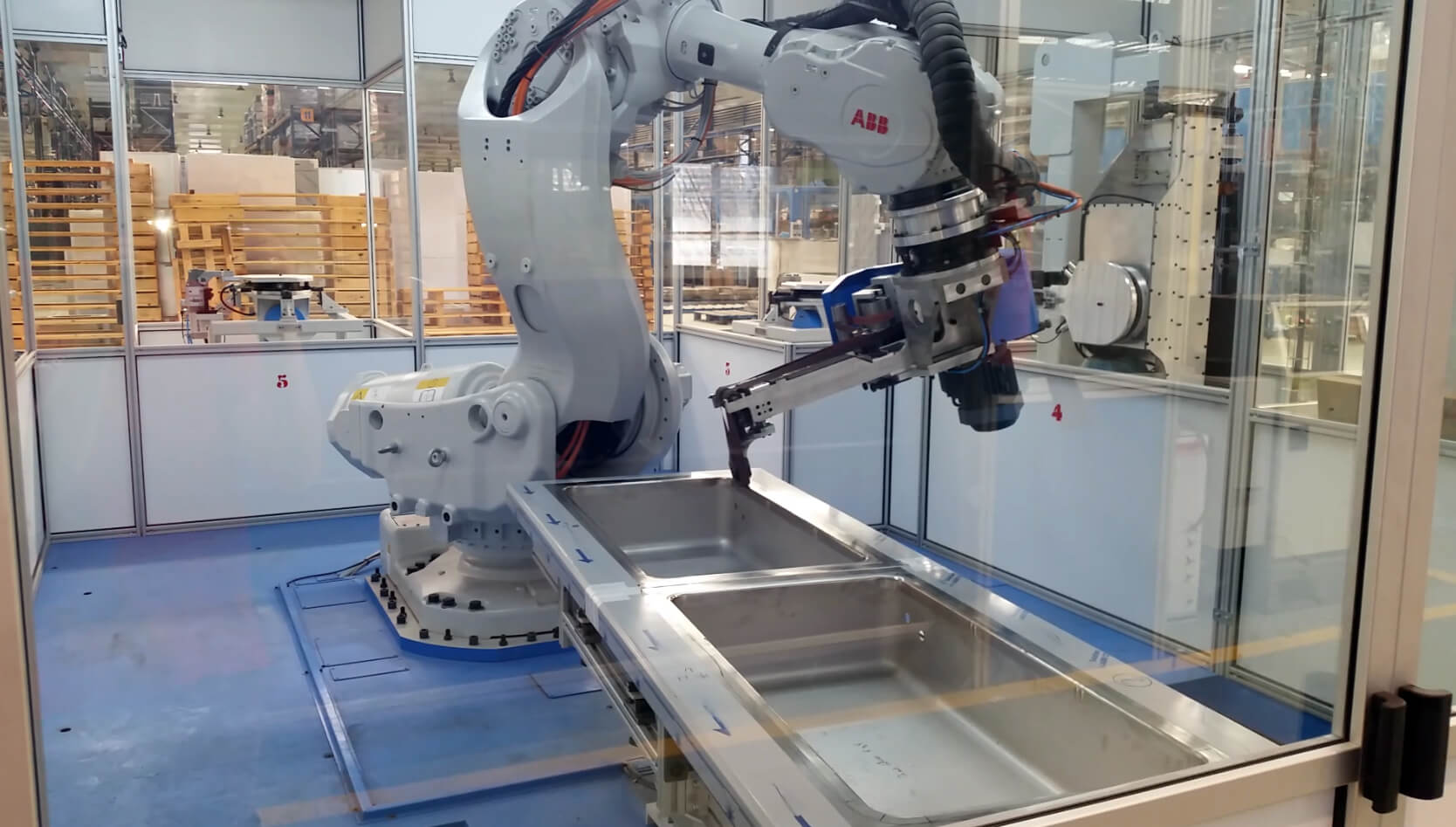
One of the benefits of working with so many companies all over the globe is you get to see a lot. I have met some amazing folks and seen so many factories I could write a book. Some of those parts and machines are below. It may be you wondered how it was done or how others do a similar process.
How about the grill for a tractor trailer? They are formed out of mill finish material and need to be mirror polished. There is a fair amount of general damage to the surface from forming as well as general handling to make it more of a challenge. There are also some complex curves to deal with.
They are finished in a CNC machine that can do two parts at a time. From more than a dozen people doing them by hand down to 11 min for a set of two to be done.
How about a fabricated sink? These can be tricky if there is a weld seam down in the bottom of the sink bowl. Some will be harder than others but there is always a solution. Weld removal if present as well as putting down the even brushed finish are the goals.
There is more than one way to do them but a common way for lower volume custom parts is with a CNC as shown. Here there was an extra axis added to the fixture to allow better access to the welds down deep in the sink bowl. They can also be done with a robot when the shape or finish need gets more complex.
Wheels? Be it an Alcoa style commercial wheel or a 28" inch or larger aftermarket wheel for pickups and cars there is a way. You can process one wheel at a time for custom low volumes or you can turn out bulk wheels in 60 to 90 seconds each depending on size and what you need.
When you need wheels and you need them fast, a rotary cell is the way to go. These machines can churn out wheels in no time at all. If you need to do both sides and you need them fast a pair of these with a robot between to do the transfer will get you wheels in no time and finished on both sides. In general this is how they are done by large OEM makers for assembly line work.
Rifle receivers? Well after they are machined there are mill lines and sharp edges O plenty. You need to remove the mill lines then polish it to a mirror for the most high end parts. There are a lot of corners you can not round over and places that are tricky to get into. The reflection of the Coke can shows how clear the finish is when done.
The sanding work is done in a dual robot cell. There is a magazine for the input and the output both. The parts enter on the left and exit on the right. The first robot completes two stages of the sanding then hands the part off to the second robot to finish. The finished part gets placed in the output magazine and rotates out when full. Its possible to keep this setup running non stop as you can load and unload while its working. When you need volume with reduced labor this will do the job.
Yes that is a subway car. There is clearly more than one way to build these, but in this case the sections needed a brushed finish. A large fixture for a large part and mobile abrasive tools move on rails to access the complete length. You need a whole lot of room for a machine like this but if you are building subway and train cars that is probably not an issue. The biggest issue here was loading and unloading. The fixture as well as the tools had to be mobile. You need to move the cars and tools away from each other far enough to get the crane in to lift out the part. Machines of this scale need flat level floors and that was the only real problem encountered.
Last one,
What if you need to finish the inside of a tank or cylinder? You use what is called a torpedo machine. The part is placed on a fixture that rotates it at an adjustable speed. Then you have an adjustable arm that can reach in and do the sanding. You need things to be rigid enough to not deflect but at the same time follow the surface. There is a lot of neat features and engineering at work here and this setup works perfect. There are also specific setups to do the domed ends of the tanks that are just as fascinating and effective.
Where there is a problem or need there is a solution. While every part and situation is unique in its own way, know you are not the first to have issues. There are answers to be had and solutions that can get you where you need to be. The best thing you can do is ask questions and as many as possible. Next is to get involved in the process and be open to ideas and suggestions. It has been shown to me many times that where there is a will there is in fact a way.
Please feel free to reach out with questions about these or other projects to get the answers you need. Every journey starts with that first step.
Topics Insidermetal finishingwheelsweld grindingRobotics