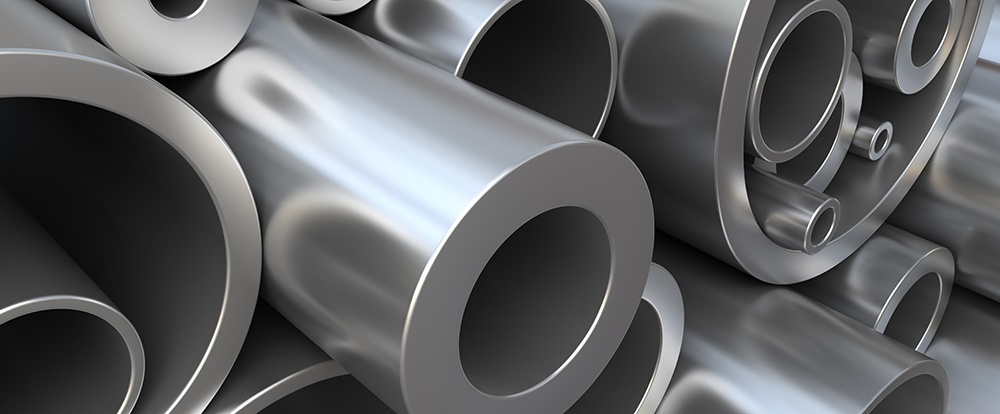
With the abundance of products incorporating tube, it's essential to provide information on how to finish it. There are numerous ways to achieve the desired results, ranging from manual processes to entry-level automation and beyond. In this post, I'll explore some of these options.
Manual:
Manual finishing can be a time-consuming and labor-intensive process, requiring skilled workers to achieve consistent results. Even with experienced workers, the finishes can still be unpredictable due to variations in technique and human error. As the volume of production increases, using manual finishing becomes less efficient and less cost-effective, leading to longer lead times and higher costs. However, for low volume or sporadic needs, manual finishing can still be a viable option, allowing for flexibility and customization when volume is not an issue. To achieve consistent results and reduce labor costs, many companies are turning to automation solutions that offer greater control and precision.
Centerless:
Centerless machines have become a common sight in tube processing as they spin the tube as it is ground down. These machines are good for removing a lot of material quickly, thanks to the abrasive being supported by a contact roller which makes it more aggressive than other options. However, working with these machines can be tricky, as a bent or bowed tube can flail around and cause damage or injury. To avoid this, it's crucial to secure the material properly before processing. It's also important to note that centerless machines are only suitable for straight lengths, as they cannot process bends. For straight length only processing these machines can be a viable option.
Planetary:
In this style machine the abrasive spins around the tube. In this case the material is pulled straight through and will not spin. With a machine like this you are able to process both straight lengths and bends. A feeding unit will take care of the straight lengths and there will be manual tooling for bends. While not as aggressive as a centerless they can still remove material when fitted with adequate abrasives for the task. As the tube is not spun they tend to be safer vs other options for processing tube. For finishing they tend to be a better option for many, smaller diameters and bows in the material are far less of an issue vs other options. These machines can be had with a single station or many depending on the need. For bowed or unpredictable material this tends to be a solid option. If you are faced with bends or touch ups it is one of the best options.
From here you move into larger more complex and costly options. From robotics to CNC finishing cells there is an answer for just about any situation. In general the planetary is a safer option where the centerless is more aggressive. For the typical handrail the planetary will do the job nicely. Nasty rusted tube with a heavy weld seam is best served with a centerless. If you are looking to get a nice even finish on reasonable quality material planetary will do nicely.
If you have questions or have a situation your dealing with related to finishing we can help. Over 40 years in finishing has allowed us to learn a great deal. We are happy to put that knowledge to work.
Topics centerless or planetary grinding systemmetal finishing