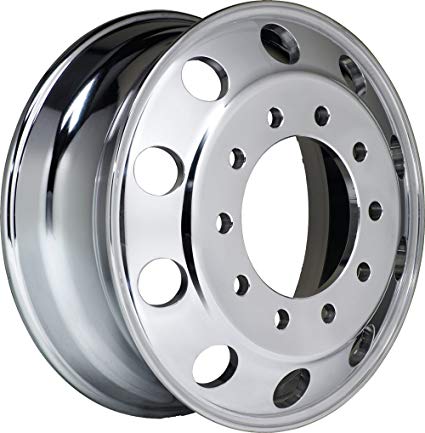
Many times we all make assumptions based on our own knowledge. This can be a very deep conversation that gets into human nature and any number of other points. But I am noting that just because you know something is no indication others do. With that thought in mind I want to go back to the basics to help every one have a good foundation to build from.
People call finishing by all kinds of names and it can be geography to generational. A common exchange example:
Person will say to me "I need to polish this tube", ok do you have a sample with a finish you want to match? "Sure here you go" I look at a tube with an 80 grit grain on it. What pops into my head is from the movie the Sandlot, Your killin me Smalls. But in that case I am in the wrong. I just assumed they knew the difference between polishing and sanding a tube. If every one calls things by different names that can be fine. Look at what Coke is called around the USA for example. I have had it called Soda, Pop, Cola and a bunch of others. In the Coke example its no problem, but if in one area they call Coke Jack Daniels that could be an issue. Sanding and polishing are two different operations with different results. Mixing the names is like calling Coke Jack Daniels.
Google can give you definitions of the words so I rather look at a more hands on version of what they are.
Polishing: This is the process that takes you to some form of a shine. You polish your car or motorcycle to get a clear shine. You can go to a fully flawless mirror or stop at just a bright finish. You would not polish your car to get a brushed or grain finish, well feel free to do you how you please but don't do it to mine. The thought of taking a scotch brite pad to a black car is going to give me nightmares now, great. The wheel below would be a good example of a polished part.
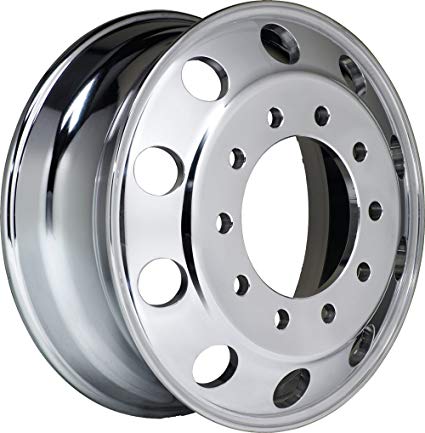
Graining: This is where you want to produce a lined or brushed type of finish. If you were to drag a brush through wet paint, the bristles produce a line pattern. That is where the brushed word seems to come from in general it seems. Your stainless steel appliances at home tend to have the grained or brushed finish. It is just a straight line pattern and nothing more. The challenge with a brushed finish is keeping it straight. If you are working with a wide belt machine the sanding belts have to move back and forth a little to stay in place on the machine. That movement can cause the finish to look like a zig zag or have a wave look to it. Below is an example of a brushed or grain finish. This is what you might find on a stainless sink or appliance.
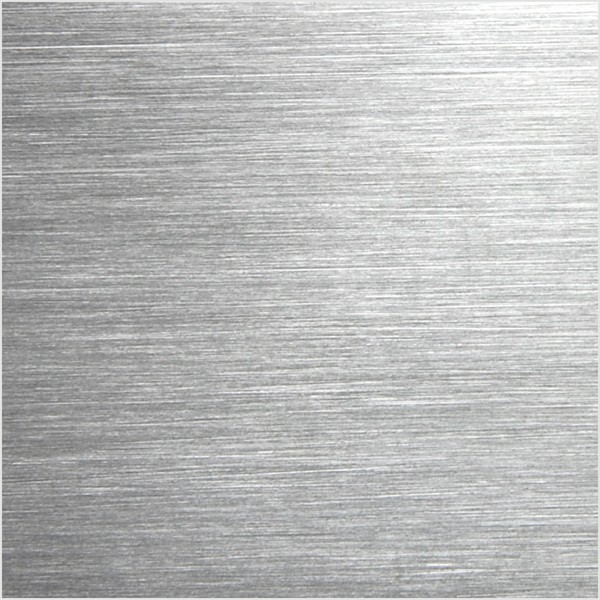
Bur removal or de burring: That is a more general situation that is more defect removal than a finish pattern. No matter how you cut metal there will be a bur. Some processes create more of a bur than others. If you push your laser too fast the bur tends to get worse. The bur is the sharp edge you can feel and cut yourself on in some cases. Taking a bur off requires two steps and no less. The first step takes the bur that is sticking straight up and bends or pushes it over to 90 degrees. The second step is a brush that will then remove that pushed over bur. If you only use a single step say in a wide belt sander you only push the bur over. Then the sanding process will create a knife edge on its own and the bur now tends to be very sharp and can cut you. If you try to just use a brush only and skip the first step you just wont remove the bur. It will be pushed down some and rounded a bit but it will still be there. In this case you would not get cut by the bur but you would be able to feel and possibly see it. Below is a close up before and after bur removal.
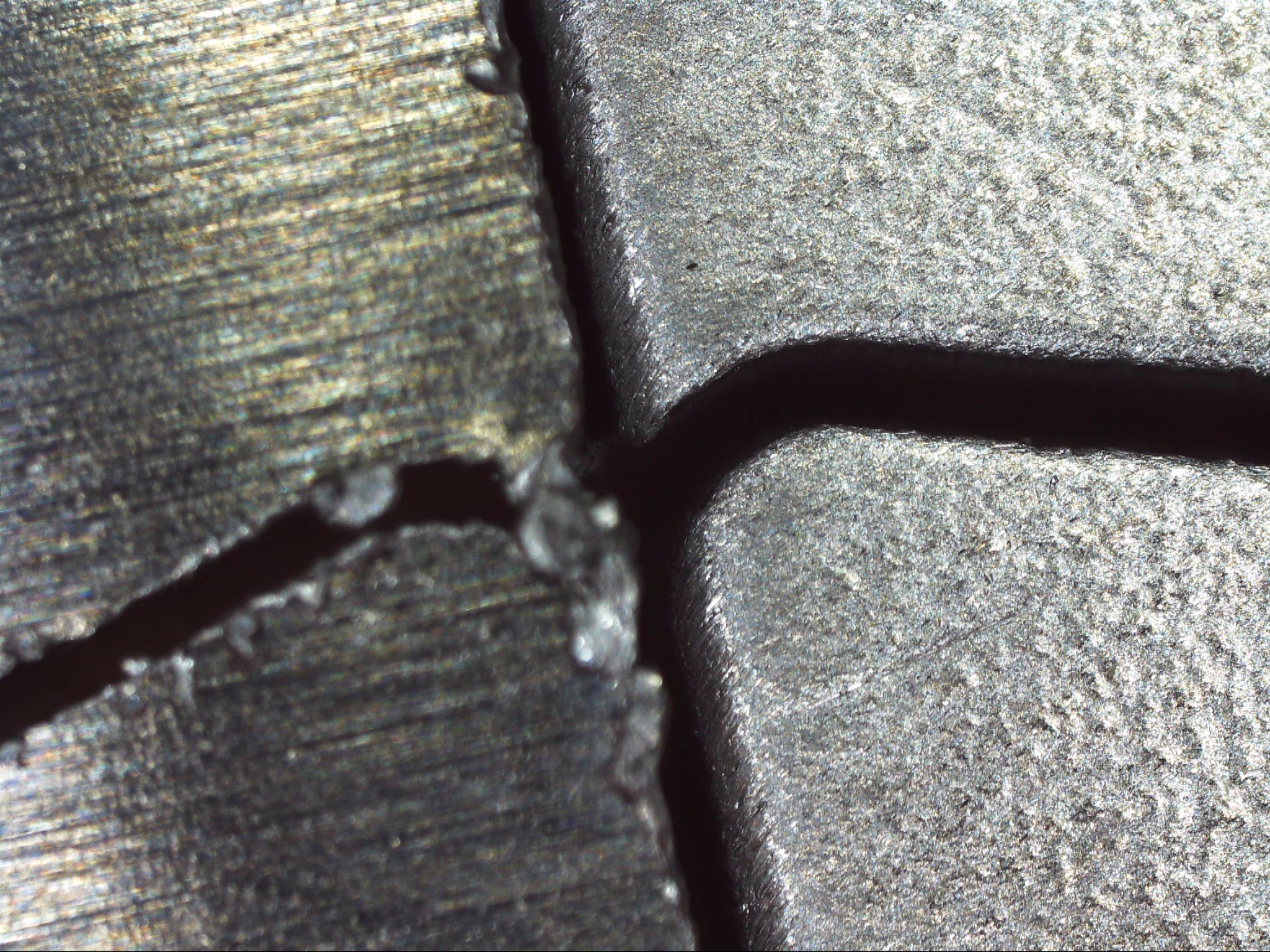
This is just some basic information to try and explain a little. If you ask your machine dealer for a polishing machine but in fact need a grained finish it is going to cause some confusion. If you are speaking to a customer and they say they need a polished finish its worth asking a few questions to be sure your on the same page. If a customer needs you to produce a part with a polished finish its going to take more time and in turn cost more. Knowing that and being sure of the finish up front will let you quote correctly and avoid having to explain a price difference later after you have made and polished a pile of parts. Don't assume people are using the same words to describe the same things. And don't assume you share the same understanding as others. Ask questions.
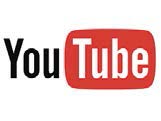
Topics tube finishingdeburring machineSmall Part Deburringwide-belt grinding machineDiscmastermetal finishingwheelspolishing