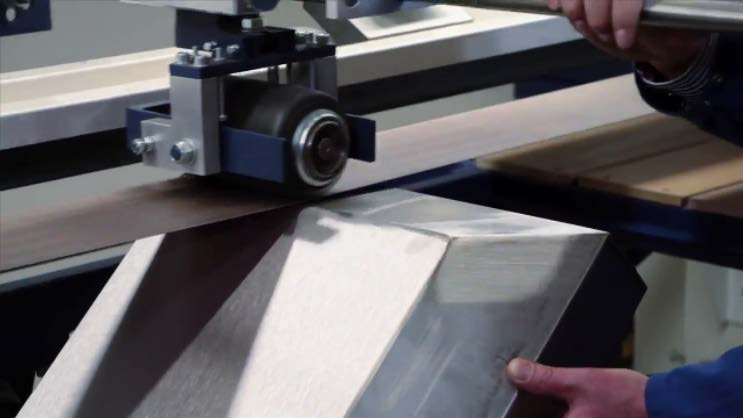
Automating a finishing process is one of the more complicated things you can take on. When it comes to finishing the definitions tend to be more in the eye of the beholder. There is not one clear standard for finishes and in some cases the end user will confuse all manner of words. It is not uncommon for companies to say they need to polish something and when you dig a bit deeper you find they need a standard #4 type grain. To them that is polishing but to someone else it would not be. This is what complicates finishing processes the most. With bending or cutting the specs and tolerances are more clearly defined for example. The labor consumed by finishing makes it a prime candidate for automation. Being able to free up 3 to 5 people by automating finishing is common and it allows the labor to be moved to other areas of need. It is also an area that tends to have poor retention as it can be some of the dirtiest work in the facility. You can gain repeatability and more consistency as well as speed while reducing labor needed and improving retention.
Starting with core products often makes the most sense as there is long term payback on the investment. Products that are physically demanding to handle or dangerous in some cases also make good candidates. Just about any process can be automated but some are far easier than others.
If you are working with people hand sanding sheet metal parts a through feed machine would cut the people needed and produce parts quickly. This would be a more simple case of automation. While more simple there are some pitfalls, ease of use and the upkeep needed are points to watch. If you reduce the labor on the processing but increase the labor on upkeep you now need the more costly staff involved more offsetting the benefit. Flexibility and simple or limited upkeep are key. The equipment produced by Loewer tick these boxes.
A fabricated enclosure would be a more complicated task as you need more than one process. To grind down the welds and then blend the finish in a single machine means you need more than one tool. This could mean something as simple as a stroke sander with an articulating mount and two belts all the way to a robot with a tool changer. Large parts with a lower volume would be better served by a stroke sander where a higher volume part could be better served by a robot or CNC system.
The best place to start is to work with some one who knows finishing first and automation second. A person that knows automation first will likely not have the background knowledge needed to put a complete solution in place. Knowing the different types of abrasive tools from simple belts all the way to compound mixtures lets you have a system that is better suited for the task as well as future growth.
The take away here is to look at your core products. Look to automate them and free up labor and improve retention. You gain better product consistency and have long term pay back on a product you depend on. Automating the core products frees up resources making you more able to deal with day to day business needs.
If you have any questions on this topic please feel free to ask as I am always happy to talk. Be it a more simple task or an incredibly complicated project I am happy to help.
Topics tube finishingdeburring machinemetal deburring machinedry deburring machineSmall Part Deburringgraining sheet metalmetal finishingpolishingautomotive