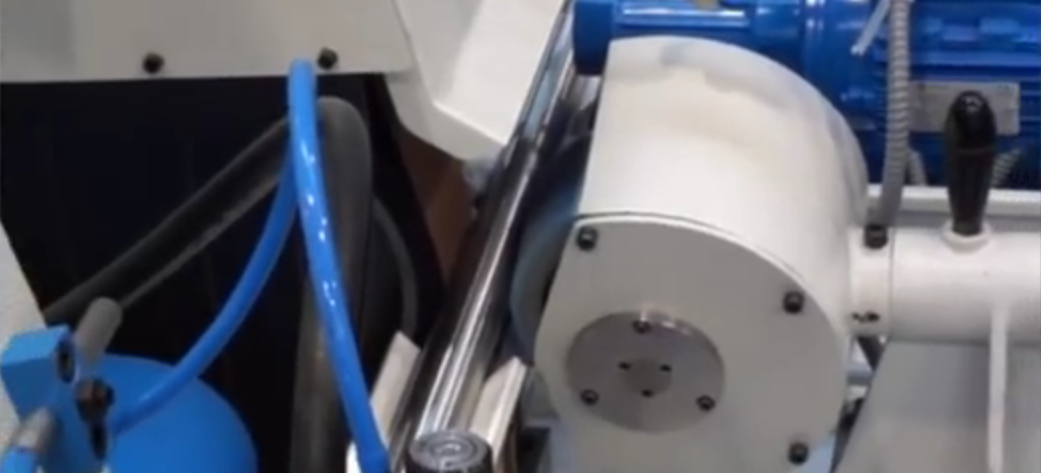
This is the second in a four-part series of blog posts about tube finishing. Click here to read part one.
In centerless grinding, a cylindrical part is supported by a work rest blade and rotated by a regulating, or feed, head.
This is different from with conventional roll grinding in which cylindrical parts are mounted on centers. Modern centerless grinding and finishing machines provide high performance, increased production rates, and improved quality at low consumable costs.
Coated abrasives offer safety, fast stock removal rates, high throughput speeds, cool operations, and performance consistency with few rejects.
Three basics of centerless grinders
Three basic elements of any centerless grinder are the grinding (or contact) head, regulating head, and work rest support.
Centerless machines vary in size and configuration, but they all operate on the same basic principles. The workpiece is constrained at all times as it travels through the machine.
As the workpiece traverses in the axial direction, it is held either by special stops, adjacent workpieces, or by the friction of the regulating head. This makes the operation suited for both long and short cylindrical pieces. The grinding head consists of the abrasive belt, the contact wheel for abrasive support, and an idler to hold belt tension. The belt direction is downward, against the workpiece, and tends to push the workpiece away and into the regulating head.
The regulating head in turn forces the workpiece back into the abrasive belt. This combination generates high unit pressures, making centerless grinding very efficient.
The regulating head rotates the workpiece at a constant surface speed and controls the through-feed of the workpiece past the abrasive belt. The regulating head can have one of two common configurations. It can consist of a belt (leather, rubber, or abrasive) running against a steel platen; or it can have a rubber or bonded-abrasive contact wheel. With either configuration, the regulating head must rotate upward, opposite the direction of the abrasive belt.
Parameters regulating head motion
Three parameters—surface speed, helix angle, and horizontal angle—govern the regulating head’s motion, and each can be adjusted to fit the specific operation. The helix angle is the head’s angle in the vertical plane parallel to the workpiece centerline. The helix angle determines how far the workpiece travels in one revolution.
Consequently, the helix angle determines how many times a given point of the workpiece comes in contact with the abrasive belt as the part passes through the machine. The actual through-speed is a function of both the helix angle and the regulating head’s rotational speed. In general, by decreasing the helix angle and increasing the regulating head speed, you can obtain a better surface finish and faster through-feed of parts.
The work rest in a centerless grinder provides firm support and properly positions the workpiece as it traverses between the regulating and grinding (contact) heads. Adjusting the work rest raises or lowers the center of the part in relation to the centerline between the contact and regulating wheel. The distance between the regulating and grinding heads controls the diameter of the workpiece.
Generally, the work rest should be positioned about one-third the distance from the grinding head to the regulating head. When determining the height position of the work rest, note that the workpiece centerline should be no more than 1⁄16 inch above the centerline of the regulating and grinding heads.
And remember to consult the operating manual or contact the machine builder for questions about specific set-up parameters.
Be sure to look for the third part of this series: Planetary Grinding Systems - A solution for Finishing Bent or Out-of-Round Tubes.
Topics centerless grinder